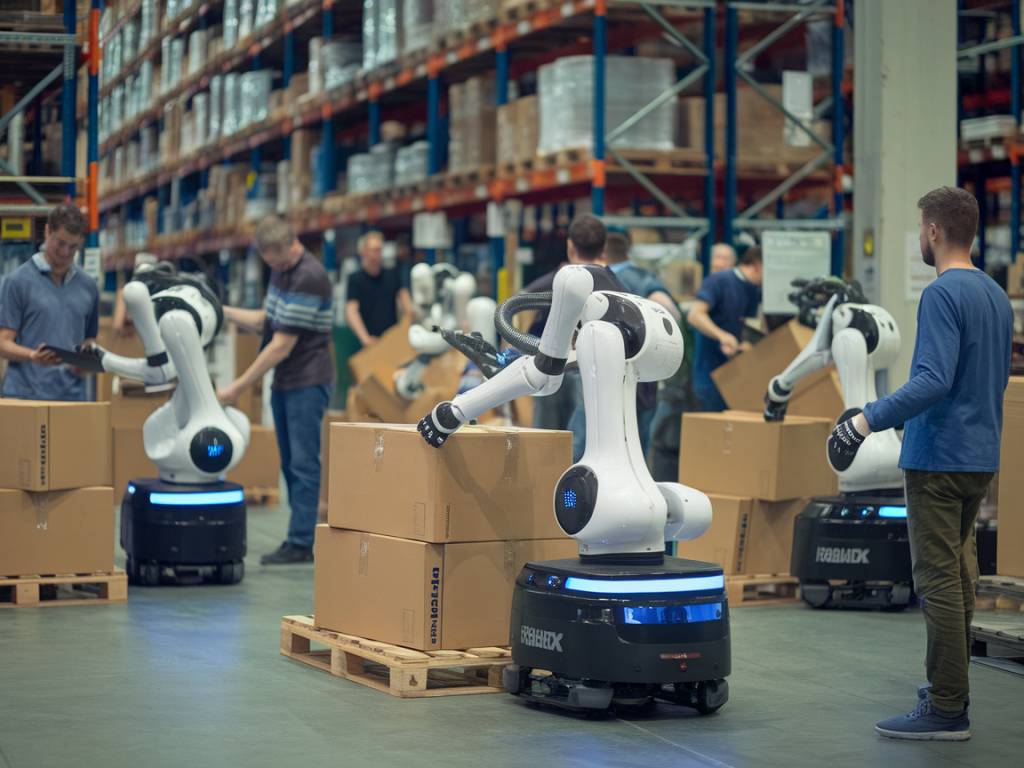
warehouse robots: reducing downtime and boosting productivity
In the ever-evolving landscape of warehouse management, robotics is playing a crucial role. Warehouse robots are increasingly being adopted in supply chain operations, mainly to reduce downtime and boost productivity. The use of warehouse robots not only enhances operational efficiency but also improves accuracy and safety. In this blog post, we will explore how warehouse robots are revolutionizing logistics and packaging.
The Rise of Warehouse Robots
The adoption of warehouse robots has surged in recent years due to advancements in robotic technology and the growing need for efficient warehouse operations. Factors such as increasing e-commerce activities, labor shortages, and the need for real-time inventory management have driven the demand for warehouse robots.
Types of Warehouse Robots
Warehouse robots come in various forms, each designed to perform specific tasks. Here are some of the most common types:
- Automated Guided Vehicles (AGVs): These robots use predefined paths to transport goods within the warehouse. They are often used to move heavy items and pallets.
- Autonomous Mobile Robots (AMRs): Unlike AGVs, AMRs navigate through dynamic environments using sensors and real-time data. They can adapt to changes in the warehouse layout.
- Sorting Robots: These robots are designed to sort items based on size, shape, and other criteria. They are commonly used in fulfillment centers to speed up order processing.
- Pick-and-Place Robots: These robots use robotic arms to pick items from shelves and place them in designated areas. They are ideal for repetitive tasks.
- Collaborative Robots (Cobots): Cobots work alongside human workers to perform tasks such as packing and palletizing. They enhance human capabilities and improve overall efficiency.
How Warehouse Robots Reduce Downtime
Reducing downtime is critical for maintaining a seamless supply chain. Warehouse robots help achieve this in several ways:
- Minimizing Human Errors: Human errors, such as misplacing items or incorrect data entry, can lead to significant downtime. Robots, on the other hand, operate with high precision and consistency, reducing the likelihood of errors.
- Continuous Operation: Warehouse robots can operate 24/7 without the need for breaks, holidays, or shift changes. This continuous operation ensures that tasks are completed faster and more efficiently.
- Efficient Maintenance: Modern warehouse robots are equipped with predictive maintenance capabilities. They can self-diagnose issues and schedule maintenance before a breakdown occurs, thus avoiding unexpected downtime.
- Optimized Workflow: Robots can analyze workflows in real-time to identify bottlenecks and optimize task allocation. This leads to a smoother and more efficient operation.
Boosting Productivity with Warehouse Robots
Productivity is a key metric in warehouse management. Warehouse robots contribute to increased productivity in several ways:
- Speed and Accuracy: Robots can complete tasks faster than human workers and with greater accuracy. This leads to quicker order fulfillment and reduced errors in order processing.
- Flexibility: Modern warehouse robots are highly adaptable. They can be reprogrammed to perform different tasks, allowing warehouses to quickly respond to changes in demand.
- Enhanced Inventory Management: Robots can perform regular inventory checks, providing real-time data on stock levels. This helps in better inventory planning and reduces the risk of stockouts or overstocking.
- Improved Worker Safety: Robots can take on dangerous or strenuous tasks, reducing the risk of workplace injuries. This leads to a safer work environment and allows human workers to focus on more value-added activities.
- Space Optimization: Robots can operate in tighter spaces and reach higher shelves compared to human workers. This allows for better utilization of warehouse space.
Challenges in Implementing Warehouse Robots
While the benefits of warehouse robots are numerous, there are also challenges to consider:
- High Initial Investment: The cost of purchasing and implementing warehouse robots can be significant. However, the long-term benefits often outweigh the initial investment.
- Integration with Existing Systems: Integrating robots with existing warehouse management systems (WMS) can be complex. Proper planning and compatibility analysis are crucial for a smooth transition.
- Training and Skill Development: Workers need to be trained to work alongside robots and manage robotic systems. This requires time and resources.
- Maintenance and Downtime: While robots reduce downtime caused by human errors, they too require maintenance and occasional repairs. Having a maintenance plan in place is essential.
Future Trends in Warehouse Robotics
The future of warehouse robotics looks promising, with several trends shaping the industry:
- AI and Machine Learning: Artificial Intelligence (AI) and Machine Learning (ML) are being integrated into warehouse robots for better decision-making and predictive analytics. This will lead to even more efficient and autonomous operations.
- Robotics as a Service (RaaS): The RaaS model allows companies to lease robots instead of purchasing them. This makes robotic solutions more accessible to smaller businesses and reduces the upfront cost.
- Collaboration Between Humans and Robots: The development of more advanced collaborative robots (cobots) will enhance the synergy between human workers and robots, leading to improved productivity and safety.
- Enhanced Mobility: Future warehouse robots will have improved mobility and navigation capabilities, allowing them to operate in more complex environments.
- 5G Connectivity: The deployment of 5G networks will enable faster and more reliable communication between robots and warehouse management systems, enhancing real-time data exchange and coordination.
In conclusion, warehouse robots are transforming the logistics and packaging industry by reducing downtime and boosting productivity. While there are challenges to implementation, the long-term benefits are significant. As technology continues to advance, the role of warehouse robots in supply chain operations will only become more prominent, leading to more efficient and innovative warehouse management solutions.