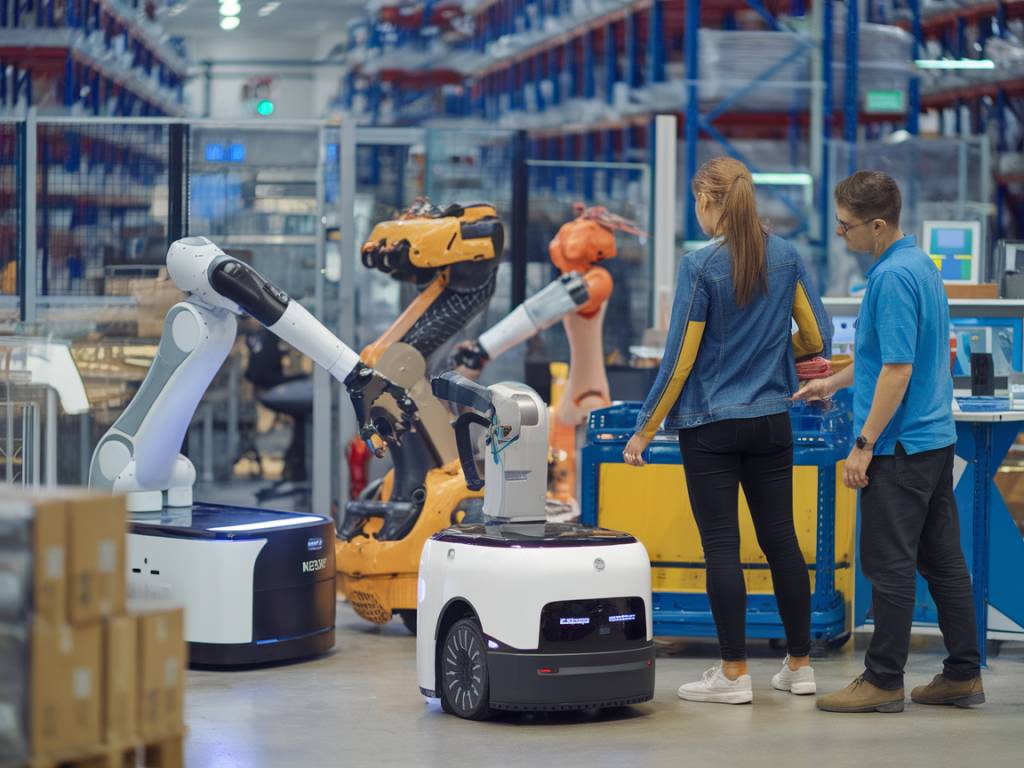
automation in distribution centers: the role of robotics in streamlining operations
In recent years, the advent of automation in distribution centers has revolutionized the logistics and supply chain industry. Among the various automation technologies, robotics has emerged as a game-changer, paving the way for more efficient, accurate, and faster operations. This article delves into the role of robotics in streamlining operations within distribution centers, exploring key aspects such as cost efficiency, accuracy, scalability, and integration.
Understanding the Need for Automation in Distribution Centers
Distribution centers are critical nodes in the supply chain, responsible for the storage, handling, and dispatching of goods. With the increasing demand for faster delivery times and greater accuracy, traditional manual processes are becoming less viable. Automation, particularly through robotics, addresses these challenges by enhancing operational efficiency and reducing human error.
The Evolution of Robotics in Distribution Centers
Robotics in distribution centers has evolved significantly over the past decade. Initially, simple robotic arms were used for basic tasks such as lifting and sorting. Today, advanced robots equipped with artificial intelligence (AI) and machine learning (ML) capabilities can perform complex tasks, including picking and packing, palletizing, and even navigating warehouse aisles autonomously.
Benefits of Robotics in Streamlining Operations
Robotics offers several benefits that contribute to the streamlining of operations in distribution centers. Here are some of the most significant advantages:
- Increased Efficiency: Robots can work 24/7 without fatigue, leading to continuous operations and higher throughput.
- Enhanced Accuracy: Advanced sensors and AI algorithms enable robots to perform tasks with precision, reducing errors significantly.
- Cost Savings: While the initial investment in robotics can be high, the long-term savings in labor costs and increased productivity often justify the expense.
- Scalability: Robotics systems can be scaled up or down based on demand, providing flexibility to handle peak periods without significant disruptions.
- Improved Safety: Robots can take over hazardous tasks, reducing the risk of workplace accidents and injuries for human workers.
Key Types of Robots in Distribution Centers
Various types of robots are utilized in distribution centers, each designed for specific tasks. Understanding these types can help businesses make informed decisions about their automation strategies. Some common types include:
- Automated Guided Vehicles (AGVs): These robots navigate using pre-defined paths and are ideal for transporting goods within the warehouse.
- Autonomous Mobile Robots (AMRs): Unlike AGVs, AMRs use advanced sensors and AI to navigate dynamic environments, making them more flexible for tasks like picking and sorting.
- Robotic Arms: Typically used for picking and packing, robotic arms can handle a variety of products with high precision.
- Palletizing Robots: These robots specialize in stacking products onto pallets, optimizing space and ensuring stability.
- Sorting Robots: Equipped with advanced vision systems, these robots can sort items based on size, weight, barcode, and other criteria.
Integration of Robotics with Warehouse Management Systems (WMS)
For robotics to effectively streamline operations, seamless integration with Warehouse Management Systems (WMS) is crucial. A WMS provides real-time data on inventory levels, order statuses, and more, which robots can use to optimize their tasks. Integration can be achieved through APIs and standardized communication protocols, ensuring that robots and WMS work in harmony to enhance efficiency.
Challenges and Considerations
While the benefits of robotics in distribution centers are clear, there are challenges and considerations to keep in mind:
- High Initial Investment: The cost of purchasing and implementing robotic systems can be prohibitive for some businesses.
- Maintenance and Downtime: Robots require regular maintenance, and any downtime can impact operations. Hence, having a reliable support system is essential.
- Workforce Training: Employees need to be trained to interact with robotic systems efficiently, which can require time and resources.
- Scalability Issues: While robots are scalable, integrating new robots or upgrading existing ones can be complex and require careful planning.
Future Trends in Robotics for Distribution Centers
As technology continues to advance, the future of robotics in distribution centers looks promising. Some emerging trends include:
- AI and Machine Learning Integration: Enhanced AI and ML capabilities will enable robots to learn and adapt to new tasks, improving their efficiency and versatility.
- Collaborative Robots (Cobots): These robots are designed to work alongside human workers, combining the strengths of both to achieve greater productivity.
- 5G Connectivity: The rollout of 5G networks will facilitate faster and more reliable communication between robots and other systems, enhancing real-time decision-making.
- Predictive Maintenance: Advanced analytics will enable predictive maintenance, reducing downtime and extending the lifespan of robotic systems.
Conclusion
In summary, the role of robotics in streamlining operations within distribution centers cannot be overstated. From increased efficiency and accuracy to improved safety and scalability, robots are transforming the logistics landscape. As technology continues to evolve, the integration of advanced robotics with other systems such as WMS will further enhance operational capabilities, making distribution centers more resilient and adaptable to changing market demands.
For businesses looking to stay competitive, investing in robotic automation is no longer just an option but a necessity. By understanding the benefits, challenges, and future trends, companies can make informed decisions and successfully navigate the complexities of modern logistics.